The field of 3D printing has witnessed remarkable growth in recent years, fueled by advancements in materials science. This paper provides a comprehensive overview of various 3D printing materials, highlighting their characteristics, advantages, and applications. From traditional polymers to cutting-edge composites, the diverse range of materials has expanded the capabilities of 3D printing technologies, making them increasingly versatile and applicable across various industries.
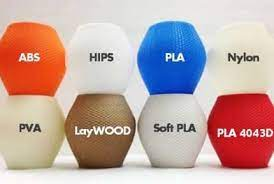
Introduction
Background
The transformative trajectory of 3D printing technologies has witnessed unprecedented growth, fueled by parallel advancements in materials science. The symbiotic relationship between technology and materials has propelled the capabilities of 3D printing, making it a ubiquitous and versatile tool across diverse domains.
Objective
This paper aspires to provide a comprehensive overview and analysis of different 3D printing materials, catering to the burgeoning demand for specialized applications. The materials covered will span traditional polymers, metals, ceramics, and emerging materials, offering a nuanced understanding of their implications for the field.
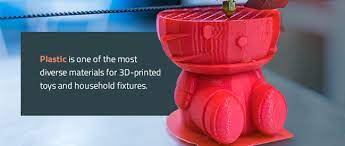
Polymers
PLA (Polylactic Acid):
PLA stands out as a biodegradable thermoplastic derived from renewable resources like corn starch. Its affordability, ease of use, and eco-friendly nature make it a staple in prototyping and consumer-oriented applications.
ABS (Acrylonitrile Butadiene Styrene):
Renowned for its durability and versatility, ABS finds applications in industrial settings and prototyping. Its capacity to strike a balance between strength and flexibility makes it a popular choice.
PETG (Polyethylene Terephthalate Glycol):
Combining the strength of ABS with the ease of PLA printing, PETG is widely employed in applications requiring high strength and transparency, making it a versatile option across industries.
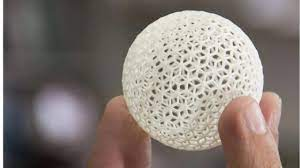
Metals
Stainless Steel:
Stainless steel, due to its corrosion resistance and mechanical properties, is a prevalent choice in aerospace, automotive, and medical applications. Its adaptability across industries underscores its importance in 3D printing.
Titanium:
Despite challenges such as high cost and intricate printing conditions, titanium’s remarkable strength-to-weight ratio and biocompatibility make it indispensable in aerospace, medical implants, and prosthetics.
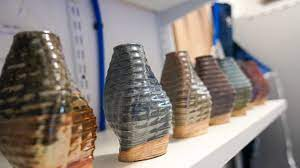
Alumina:
Alumina ceramics, known for their hardness, wear resistance, and thermal stability, find applications in diverse fields, including dental prosthetics and electronic components.
Zirconia:
Zirconia ceramics, characterized by high strength, fracture toughness, and biocompatibility, play pivotal roles in dental crowns, implants, and aerospace components.
Emerging Materials
Biocompatible Polymers:
Materials such as PEEK (Polyether Ether Ketone) and ULTEM (Polyetherimide) are gaining prominence in the medical field for their biocompatibility and sterilization capabilities.
Advanced Composites:
The rise of composite materials, including carbon fiber-reinforced polymers, showcases the industry’s pursuit of enhanced strength and lightweight properties. These composites are making significant inroads in aerospace, automotive, and sports equipment manufacturing.
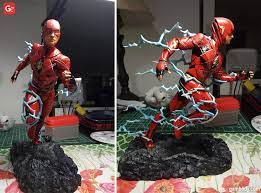
Conclusion
This paper has undertaken an extensive exploration of various 3D printing materials, elucidating their distinct advantages and applications. As 3D printing technology advances, the synergistic progress of materials will undoubtedly unlock innovative solutions across industries. A nuanced understanding of material properties is pivotal for selecting the right material for specific applications, propelling additive manufacturing into new realms of possibility. This holistic approach positions 3D printing as an ever-evolving frontier, continually pushing the boundaries of what can be achieved across diverse domains.